尽管光线条件不佳依然可以拍摄清晰的照片,拍摄快照而不模糊,识别交通标志和道路标记,或利用特定系统识别危险情况-所有这一切如今都可以借助于现代相机而得以实现。然而相机或智能手机的静态和视频图像质量究竟如何?并且与其他供应商的型号相比又如何呢?
最终用户、智能手机和相机制造商、汽车或航空航天、医疗与安全或自动化技术领域的公司-他们都对静态和视频图像的质量提出了较高的要求,并积极寻求这些问题的答案。
DxOMark Image Labs公司直面这些问题并寻求提供解决之道。该公司为客户提供咨询服务和完整的图像质量测试实验室解决方案。此类解决方案由硬件、软件和测试协议组成,并且可确保可重复的、与操作人员无关的结果。DxOMark Image Labs市场营销副总裁Nicolas Touchard在接受PI Karlsruhe的采访中,介绍了评估静态和视频图像质量的方法以及如何在图像稳定技术的测试中使用PI六足位移台。
有哪些关键的图像质量属性?
根据特定的关键图像质量属性评估每台相机。图像质量属性包括分辨率、对比度、颜色、纹理、缩放、自动对焦、曝光和图像稳定等。对于每一项属性,均拍摄并评估数千幅图像以获取具有统计意义的结果。为了使图像质量具有可比性,必须始终在相同条件下采用相同的方法测试相机和相机组件。DxOMark评估所依据的测量方法是与在IEEE / CPIQ和ISO TC42-WG18等国际标准化工作组中开展合作的成像行业内的数家公司共同开发的。
图像稳定测试– PI六足位移台模拟相机运动
图像稳定测试评估内置于相机中的光学和电子图像稳定系统的工作情况。这些系统旨在补偿运动,因此避免了模糊图像。
在与图像稳定相关的所有测试程序中,相机在多根轴上的重复精度非常重要。“我们必须确保每次测试的模拟频率和运动都是相同的,例如围绕旋转轴θX、θY、θZ(俯仰、偏航、滚转),”Nicolas Touchard强调说。例如,在测试相机和智能手机时,需要高达约12赫兹的频率来模拟人手的颤抖,而驾驶辅助系统中的图像稳定则需补偿更高的频率。
A deeper dive
Two alignment techniques are most useful today: area scans, and gradient searches for fast optimization and tracking.
Area scans
A good example of a legacy approach to an area scan is a classical raster or serpentine scan, which sweeps one axis, then increments its orthogonal axis, and repeats until the area is covered. Variations on this theme are common, including stepwise hill-climbs. But these approaches pose fundamental issues today. The stopping-and-starting adds settling time and causes vibration throughout the system, and the linear acquisitions can lead the system to actually de-align in common situations of asymmetric coupling profiles.
By comparison, PI’s firmware-based area scans use smooth, continuous sinusoidal and spiral patterns of selectable frequency. So system resonances can easily be avoided, allowing the non-stop scan to proceed without vibration. The result is considerably higher speed. Add built-in modelling in some controllers, and the system can determine the peak (or even the centroid of a top-hat coupling) with good accuracy and speeds down to a few hundred milliseconds.
Gradient search
The digital gradient search was first developed in 1987 and, until now, has been mostly unchanged in its implementation through four subtle generations of the technology. A small, circular motion causes the coupling signal (or other figure-of-merit) to vary, and this variation can be analysed in phase and amplitude to determine the instantaneous gradient. This allows a fast and direct path to optimum, with tracking possible for appropriate mechanisms.
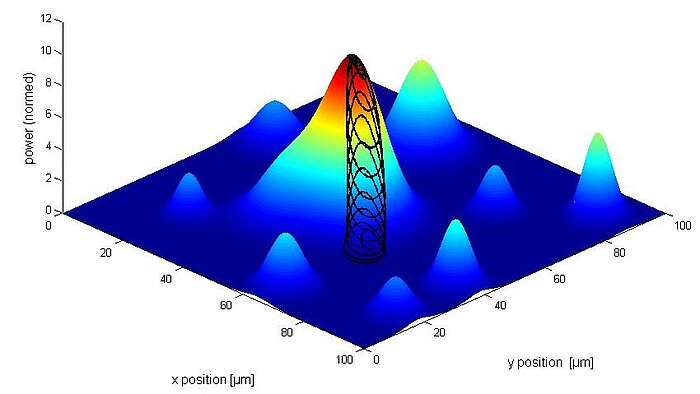
PI’s radical fifth-generation approach builds on this classical foundation to enable multiple gradient searches to proceed in parallel. For example, this allows an XY lock-on to be performed at the same time a theta-Z optimization runs— an essential combination for any array-device alignment. This fast, parallel execution replaces the time-consuming iterative loop of separate XY and theta-Z alignments that was formerly required. One step instead of dozens!
PI´s latest breakthrough
Since 2016, firmware-based fast area scan, gradient search and parallel gradient-search technologies have been implemented in PI’s powerful piezo nanopositioner and hexapod controllers. Now fast alignment functionality is available for ACS controls. Combined with PI’s large industrial stages (including spindle-driven and linear-motor stages, gantries and air-bearing assemblies), this forms a foundation for especially high-throughput applications involving large-area processing, such as when devices are processed in trays, or across several stations, or on an indexing platform or conveyor.
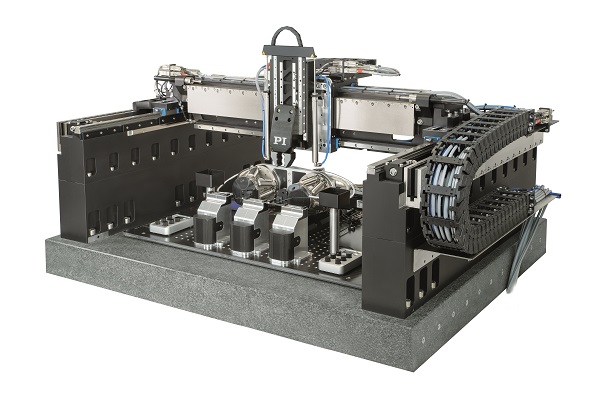
ACS controls lead the industry in modularity and performance. Based on an EtherCAT open, distributed architecture, they support absolute encoders, minimizing system start up times, easing initialization approaches and reducing collision risks. ACS’ yaw control (combined with PI’s highly optimized joint construction) provides industry-leading orthogonality correction and minimizes risk of axis binding—a distressingly common issue for older architectures. True MIMO gantry control plus dynamic cross axis control yields uniform performance over the gantry area, eliminating grid-based approximation methods and their consequent lowest-common-denominator approach to tuning over large areas. Together, these mean higher performance and reproducibility in your application.
These benefits come with PI’s and ACS’ rich offering of global support options, ranging from on-site Quick Start and training, to extended warranties and service plans, to consulting and co-engineering, to application and software consultation and quick-port approaches for key customers transiting from other architectures.
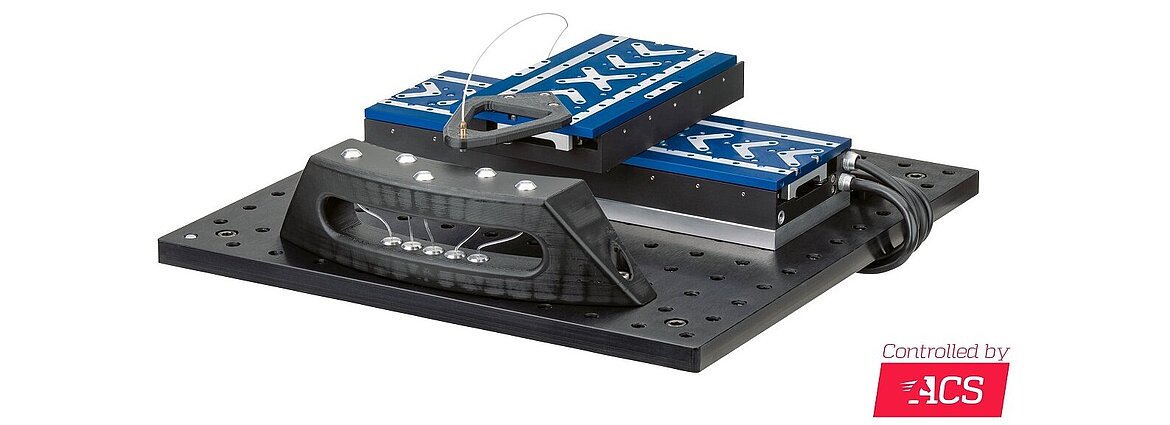
Summary
Photonics today is serious business, with a rapid rate of innovation and churn and broad adoption by important semiconductor and networking players. Manufacturing and testing these devices demand flexibility and high performance from production systems and tooling. Multiple studies have spotlighted alignment time as the highest cost contributor to photonic device fabrication, both from the lengthy process times formerly required and from the repeating requirement for alignment throughout the production process. PI’s revolutionary fast alignment technology is unmatched for meeting these challenges, and now it is deployed in large-area mechanisms based on a modular, open-architecture approach ideal for systems integration and tooling platforms.