单面光子学对准系统,含H-811六足位移台及NanoCube纳米定位器;带4个模拟量输入的E-712数字控制器;带2个模拟量输入的C-887六足位移台控制器;极速对准固件程序;软件包
F-712.Hxx 紧凑型高速六自由度光子学对准系统
单面/双面、直立式/超薄设计全自动阵列对准程序
- 集成适用于硅光子晶圆、光子器件、光子集成电路及光纤的扫描/对准程序
- 强大的阵列对准算法
- 跨多设备、I/O及自由度的快速同步优化
- 提供广泛深入的软件支持,兼容Windows和Linux系统C#、Python、LabVIEW及MATLAB等主流编程语言
- 典型自动对准时间<0.5s
- PI全球团队提供快速应用与产品支持
解决问题
PI快速多通道光子对准(FMPA)解决方案整合了针对应用优化的量产级高动态对准平台与精密控制器,集成了全球先进的首道光搜索、轮廓分析及功率优化对准算法。
对准时间减少99%
该获奖技术解决了光子测试与组装的首要成本痛点: 各元件与通道所需的精密对准。 传统对准技术可追溯至上世纪80年代,对准时间长达数分钟。 PI快速光学对准方案通常可将对准时间减少99%,常规任务可在1秒内完成。 研究表明,在FMPA出现之前,光子器件约80%的成本消耗在对准上。FMPA将对准时间减少99%,可以节约这部分的成本,显著提升了生产经济效益。 随着新型应用与设备的涌现,光子元件需求预计将在短期内增长三个数量级,而FMPA正是实现这一目标的核心赋能技术。
经市场验证的多功能、紧凑型解决方案,应对六自由度对准难题
这些集成方案整合了PI旗舰紧凑型六足位移台与高动态、超分辨率NanoCube压电快速扫描台,提供六自由度定位、扫描与优化。 自2016年问世以来,这些独特的微型机器人解决方案已广泛用于硅光子晶圆探测、阵列对准及光子器件自动化装配等多种应用,并成为众多顶尖OEM厂商与内部集成团队的首选。 应用千变万化,但选择的理由很简单:革命性的对准速度,将生产吞吐量提升两个数量级;易于掌握的指令集,广泛深入的软件支持;以及全球应用经验与服务体系。
协同增效,提升性能
六足位移台与NanoCube机构协同工作,实现多通道、I/O及自由度的同步优化,并在所有自由度与I/O间实现并行优化。 例如:NanoCube通过柔性铰链导向与PICMA压电陶瓷驱动器实现极高的速度与长使用寿命,而六足位移台则提供大范围行程,含俯仰-偏转-旋转定位及对准优化功能,适用于阵列波导等应用场景。 高分辨率模拟输入接口可连接功率测量设备(如PI F-712.PM1高带宽光功率计),实现优化与轮廓分析功能,支持高效快速的自动化光纤对准。 系统支持软限位功能,确保过程安全。
超薄设计与直立式配置
PI六自由度光纤对准系统包含F-712.HA1、F-712.HA2和F-712.HU1三种标准配置。
F-712.HA1单侧倾斜式与F-712.HA2双侧倾斜式配置均具有超薄结构。 凭借六足位移台的倾斜安装特性,可贴近(甚至低于)安装表面执行对准操作, 是硅光子晶圆探测应用的理想选择。
F-712.HU1单侧直立式配置尤其适用于器件特性测试与封装工艺。 可按需定制双面或多面直立式配置方案。
基于这些精密平台,可快速配置支持亚微米级晶圆接近自动化等功能的超高速对准解决方案。
应用领域
光子集成电路生产、光纤阵列/准直器/光学元件/透镜对准、硅光子晶圆检测、光子与光纤器件的测试/组装/封装
规格
规格
运动和定位 | F-712.HA1 | F-712.HA2 | F-712.HU1 | 公差 |
---|---|---|---|---|
主动轴的数量 | 9 | 18 | 9 | |
主动轴,粗定位 | X ǀ Y ǀ Z ǀ θX ǀ θY ǀ θZ | X ǀ Y ǀ Z ǀ θX ǀ θY ǀ θZ | X ǀ Y ǀ Z ǀ θX ǀ θY ǀ θZ | |
X向上的行程,粗定位 | 13 mm | 13 mm | 34 mm | |
Y向上的行程,粗定位 | 32 mm | 32 mm | 32 mm | |
Z向上的行程,粗定位 | 17 mm | 17 mm | 13 mm | |
X向上的最小位移,粗定位 | 0.1 µm | 0.1 µm | 0.1 µm | |
Y向上的最小位移,粗定位 | 0.1 µm | 0.1 µm | 0.1 µm | |
Z向上的最小位移,粗定位 | 0.1 µm | 0.1 µm | 0.05 µm | |
X向上的最大速度,粗定位,空载 | 10 mm/s | 10 mm/s | 10 mm/s | |
Y向上的最大速度,粗定位,空载 | 10 mm/s | 10 mm/s | 10 mm/s | |
Z向上的最大速度,粗定位,空载 | 10 mm/s | 10 mm/s | 10 mm/s | |
θX向上的旋转范围,粗定位 | 29 ° | 29 ° | 20 ° | |
θY向上的旋转范围,粗定位 | 20 ° | 20 ° | 20 ° | |
θZ向上的旋转范围,粗定位 | 20 ° | 20 ° | 42 ° | |
驱动器类型,粗定位 | 无刷直流电机 | 无刷直流电机 | 无刷直流电机 | |
传感器类型,粗定位 | 旋转编码器 | 旋转编码器 | 旋转编码器 | |
主动轴,精定位 | X ǀ Y ǀ Z | X ǀ Y ǀ Z | X ǀ Y ǀ Z | |
X向上的行程,精定位 | 100 µm | 100 µm | 100 µm | |
Y向上的行程,精定位 | 100 µm | 100 µm | 100 µm | |
Z向上的行程,精定位 | 100 µm | 100 µm | 100 µm | |
X向上的开环最小位移,精定位 | 0.3 nm | 0.3 nm | 0.3 nm | |
Y向上的开环最小位移,精定位 | 0.3 nm | 0.3 nm | 0.3 nm | |
Z向上的开环最小位移,精定位 | 0.3 nm | 0.3 nm | 0.3 nm | |
X向上的闭环最小位移,精定位 | 2.5 nm | 2.5 nm | 2.5 nm | |
Y向上的闭环最小位移,精定位 | 2.5 nm | 2.5 nm | 2.5 nm | |
Z向上的闭环最小位移,精定位 | 2.5 nm | 2.5 nm | 2.5 nm | |
标称量程内的线性误差 | 2 % | — | — | max. |
X向上的双向重复精度,10%行程 | 2 nm | 2 nm | 2 nm | typ. |
Y向上的双向重复精度,10%行程 | 2 nm | 2 nm | 2 nm | typ. |
Z向上的双向重复精度,10%行程 | 2 nm | 2 nm | 2 nm | typ. |
驱动器类型,精定位 | PICMA | PICMA | PICMA | |
传感器类型,精定位 | 增量直线光栅尺 | 增量直线光栅尺 | 增量直线光栅尺 | |
调整 | F-712.HA1 | F-712.HA2 | F-712.HU1 | 公差 |
螺旋区域扫描10µm直径的扫描时间 | < 0.2 s | < 0.5 s | < 0.2 s | typ. |
螺旋区域扫描100µm直径的扫描时间 | < 0.3 s | < 1 s | < 0.3 s | typ. |
螺旋区域扫描500µm直径的扫描时间 | < 2 s | < 5 s | < 2 s | typ. |
通过梯度搜索进行信号优化,±5µm的随机化(重复精度< 0.01dB) | 0.3 s | 0.3 s | 0.3 s | |
光学功率计的要求 | F-712.HA1 | F-712.HA2 | F-712.HU1 | 公差 |
输出信号 | 模拟量输出,由线性向对数式的完美转换 | 模拟量输出,由线性向对数式的完美转换 | 模拟量输出,由线性向对数式的完美转换 | |
最大输出电压范围 | –5至5 V | –5至5 V | –5至5 V | max. |
最小带宽 | 1 kHz | 1 kHz | 1 kHz | min. |
最大噪声级 | -60 dBm | -60 dBm | -60 dBm | max. |
线性误差说明:未采用多项式线性化处理
扫描时间:扫描整个区域并移至最大强度的典型时间跨度
梯度搜索信号优化:首次寻光后即可达到全局最大值
工作温度范围说明:该数值适用于机械部件;控制器工作温度范围:5至40℃
可咨询定制版本。
测量定位的规格时,使用典型速度。 数据以测量报告的形式包含在产品交付中,并存储在PI中。
各个坐标(X、Y、Z、θX、θY、θZ)的最大行程范围是相互依存的。 各个坐标(X、Y、Z、θX、θY、θZ)的最大行程范围是相互依存的。当所有其他轴都处于标称行程范围的零位置并且使用默认坐标系时,或者更确切地说,当旋转中心点设置为0,0,0时,每个轴的数据显示其最大行程范围。
有关默认坐标系和六足位移台的枢轴点坐标,请参见尺寸图。 改变枢轴点将缩短θX、θY和θZ向上的行程。 改变坐标系的方向(如当光轴要为Z轴时)将改变X、Y和Z向上的行程。
测量定位的规格时,使用典型速度。数据以测量报告的形式包含在产品交付中,并存储在PI中。
各个坐标(X、Y、Z、θX、θY、θZ)的最大行程范围是相互依存的。当所有其他轴都处于标称行程范围的零位置并且使用默认坐标系时,或者更确切地说,当旋转中心点设置为0,0,0时,每个轴的数据显示其最大行程范围。
PI技术数据是在22±3°C环境温度下定义的。除非有特别说明,所有数值均基于无负载的情况。某些性能参数是相互关联的。“typ.”标识 是指属性的统计平均值,并非承诺每个交付产品均达到该数值。在产品交付前的最后检验中,我们只检测选定的属性,而不是全部属性。请注意,产品的某些特性可能会随着使用时间的增长而逐渐下降。
下载
产品注解
数据表
文件
用户使用手册F712T0024
F-712.HP1安装适配器,适用于F-712.HA1/F-712.HA2光纤对准系统
用户使用手册F712T0003
用于快速多通道光子学对准的六自由度F-712.HA1和F-712.HA2系统。硬件描述。
用户使用手册E712T0016
快速多通道光子学对准系统(FMPA)
用户使用手册F712T0019
光功率的计算 - 使用F-712.PM1功率计和F-712高精度光纤对准系统
用户使用手册F712T0007
F-712.HU1六自由度快速对准系统
3D模型
F-712.Hxx 3D模型
F-712.Hxx 3D模型
白皮书
Case Study: Photonic Array Device Assembly
报价/订购
就所需数量、价格和供货周期请求免费报价或描述您所需的改型。
双面光子对准系统,含2个H-811六足位移台及2个NanoCube纳米定位器;带4个模拟量输入的E-712数字控制器;2个各带2个模拟量输入的C-887六足位移台控制器;极速对准固件程序;软件包
单面光子对准系统,含H-811六足位移台及NanoCube纳米定位器,直立式配置;带4个模拟量输入的E-712数字控制器;带2个模拟量输入的C-887六足位移台控制器;极速对准固件程序;软件包
如何获取报价
询问工程师
通过电子邮件或电话从当地PI销售工程师处快速获取解答。
技术
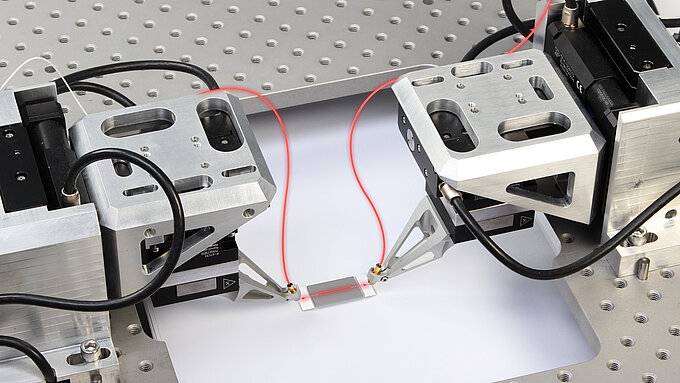
主动对准
在众多领域中,兴起了将器件对准至纳米级精度的需求。诸如小型照相机中的镜头或镜头组件等光学部件乃至CCD芯片自身,均需要以更高的精度进行定位。

PI产品的EtherCAT连接性
PI提供高精度驱动器,其可用作EtherCAT从控制器,或与ACS运动控制器集成后用作主控制器,或在现有结构中用作第二主控制器。
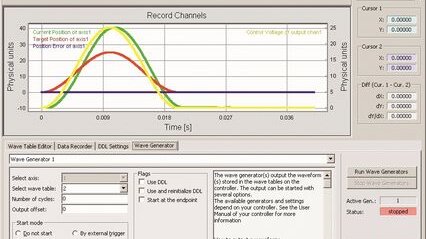
数字运动控制器
数字技术为提高不存在于传统模拟技术的控制工程的性能开辟了可能性。
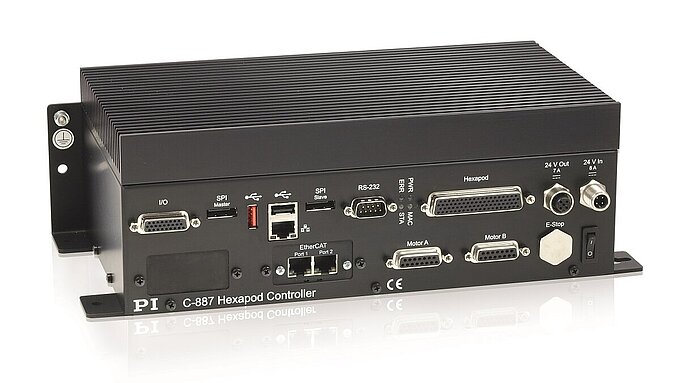
数字和模拟接口
高速USB或TCP/IP接口以及RS-232是PI现代数字控制器支持的标准接口。此外,PI也提供数字或模拟实时能力接口。
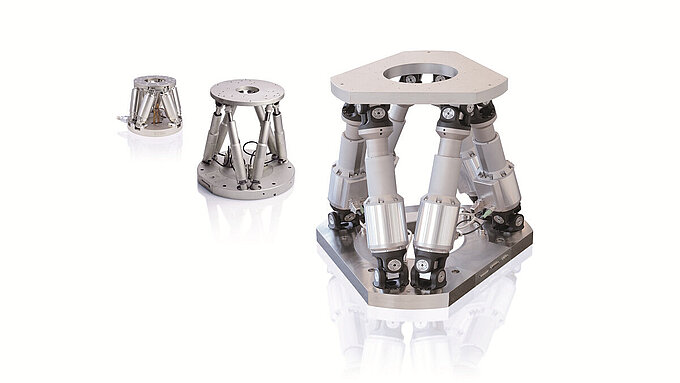
多轴定位器
六足位移台平台适用于在所有六个自由度(即三根线性轴和三根旋转轴)实现负载的准确定位和校准。