小型六足位移台;无刷直流电机;真空兼容至10-6hPa;有效载荷为5kg;速度为10mm/s;电缆长度为2m(真空侧);真空接头。 空气端连接电缆不包含在发货范围内,需单独订购。
H-811.I2V 真空兼容小型六足位移台
紧凑、高精度
- 真空:10-6hPa
- 行程:±17mm / ±16mm / ±6.5mm
- 旋转范围:±10° / ±10° / ±21°
- 最小位移:0.2µm / 0.2µm / 0.08µm
- 重复精度:±0.06µm
- 有效载荷:5kg
应用领域
H-811占地面积小,其真空型号完美适配真空室内的安装需求。 其高精度特性使H-811.I2V能以高精度和效率执行对准流程。 在此类应用中,它可显著提升复杂制造工艺和测量流程的效率。
高动态性能与杰出可靠性的结合
该六足位移台采用并联运动结构,可在超紧凑设计下实现六自由度运动。 得益于无刷直流电机和高刚性机械设计,即使在存在外部干扰时(如胶合工艺),H-811仍能满足主动对准应用所需的动态性能。 丰富的软件工具通过简化系统调试流程,并提供外部模拟控制信号自动对准子程序,为用户提供支持。
运动仿真保护总体系统
PIVirtualMove软件(可免费下载)模拟H-811的行程、对准及允许的力和扭矩,便于优化系统配置。 在此过程中,将同时考虑选定的旋转中心与负载重心。
六足位移台控制器发货时提供免费软件包,内含工件和刀具坐标系及仿真工具, 这些工具有助于保护光学或光子器件等关键组件。
规格
规格
运动 | H-811.I2V | 公差 |
---|---|---|
主动轴 | X ǀ Y ǀ Z ǀ θX ǀ θY ǀ θZ | |
X向上的行程 | ± 17 mm | |
Y向上的行程 | ± 16 mm | |
Z向上的行程 | ± 6.5 mm | |
θX向上的旋转范围 | ± 10 ° | |
θY向上的旋转范围 | ± 10 ° | |
θZ向上的旋转范围 | ± 21 ° | |
X向上的最大速度 | 10 mm/s | |
X向上的典型速度 | 5 mm/s | |
Y向上的最大速度 | 10 mm/s | |
Y向上的典型速度 | 5 mm/s | |
Z向上的最大速度 | 10 mm/s | |
Z向上的典型速度 | 5 mm/s | |
θX向上的最大角速度 | 250 mrad/s | |
θX向上的典型角速度 | 120 mrad/s | |
θY向上的最大角速度 | 250 mrad/s | |
θY向上的典型角速度 | 120 mrad/s | |
θZ向上的最大角速度 | 250 mrad/s | |
θZ向上的典型角速度 | 120 mrad/s | |
定位 | H-811.I2V | 公差 |
X向上的最小位移 | 0.2 µm | typ. |
Y向上的最小位移 | 0.2 µm | typ. |
Z向上的最小位移 | 0.08 µm | typ. |
θX向上的最小位移 | 2.5 µrad | typ. |
θY向上的最小位移 | 2.5 µrad | typ. |
θZ向上的最小位移 | 5 µrad | typ. |
X向上的单向重复精度 | ± 0.15 µm | typ. |
Y向上的单向重复精度 | ± 0.15 µm | typ. |
Z向上的单向重复精度 | ± 0.06 µm | typ. |
θX向上的单向重复精度 | ± 2 µrad | typ. |
θY向上的单向重复精度 | ± 2 µrad | typ. |
θZ向上的单向重复精度 | ± 3 µrad | typ. |
X向上的空回 | 0.2 µm | typ. |
Y向上的空回 | 0.2 µm | typ. |
Z向上的空回 | 0.06 µm | typ. |
θX向上的空回 | 2 µrad | typ. |
θY向上的空回 | 2 µrad | typ. |
θZ向上的空回 | 4 µrad | typ. |
驱动性能 | H-811.I2V | 公差 |
驱动类型 | 无刷直流电机 | |
机械性能 | H-811.I2V | 公差 |
X向上的刚性 | 0.7 N/µm | |
Y向上的刚性 | 0.7 N/µm | |
Z向上的刚性 | 8 N/µm | |
最大负载能力,底板沿水平方向 | 5 kg | |
最大负载能力,底板沿任意方向 | 2.5 kg | |
最大保持力,底板沿水平方向 | 15 N | |
最大保持力,底板沿任意方向 | 2.5 N | |
总质量 | 2.2 kg | |
材料 | 不锈钢,铝 | |
其他 | H-811.I2V | 公差 |
工作温度范围 | 0至50 °C | |
真空等级 | 10⁻⁶ ǀ hPa | |
最高耐温 | 80 °C | |
数据传输连接器 | HD D-sub 78针(公头) | |
电源电压连接器 | LEMO | |
电缆长度 | 2 m | |
电源电缆外径 | 4.7 mm | |
固定装置的最小弯曲半径,电源 | 50 mm | |
数据传输电缆外径 | 6.6 mm | |
固定装置的最小弯曲半径,数据传输 | 70 mm | |
推荐控制器/驱动器 | C-887.5x |
H-811.I2V标配电缆不是拖链兼容型电缆。
有关数据传输电缆外径的注意事项:数据传输连接由两根末端共用一个接头的电缆组成。 标称直径为每根电缆的直径。
空气端连接电缆不包含在发货范围内,需单独订购。
在真空环境下持续运行时,由于发热可能需要限制运行参数。
测量定位的规格时,使用典型速度。数据以测量报告的形式包含在产品交付中,并存储在PI中。
各个坐标(X、Y、Z、θX、θY、θZ)的最大行程范围是相互依存的。当所有其他轴都处于标称行程范围的零位置并且使用默认坐标系时,或者更确切地说,当旋转中心点设置为0,0,0时,每个轴的数据显示其最大行程范围。
PI技术数据是在22±3°C环境温度下定义的。除非有特别说明,所有数值均基于无负载的情况。某些性能参数是相互关联的。“typ.”标识 是指属性的统计平均值,并非承诺每个交付产品均达到该数值。在产品交付前的最后检验中,我们只检测选定的属性,而不是全部属性。请注意,产品的某些特性可能会随着使用时间的增长而逐渐下降。
下载
产品注解
Product Change Notification H-811.I2V
数据表
文件
3D模型
H-811.I2V 3D模型
软件档案
PIVirtualMove
如何获取报价
询问工程师
通过电子邮件或电话从当地PI销售工程师处快速获取解答。
技术

PI产品的EtherCAT连接性
PI提供高精度驱动器,其可用作EtherCAT从控制器,或与ACS运动控制器集成后用作主控制器,或在现有结构中用作第二主控制器。
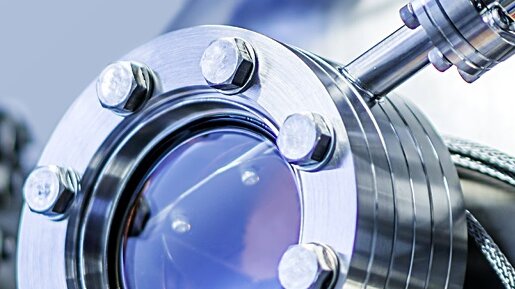
真空
认真处理、充足空间:PI不仅具有验定材料、部件和最终产品的必要设备,同时也具有高真空和超高真空定位系统方面的多年经验。
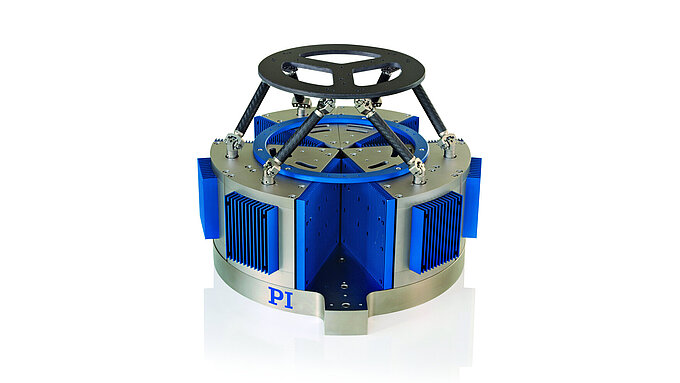
六足位移台用作运动模拟器
运动模拟器具对运动动力学具有较高的要求(振动器)。
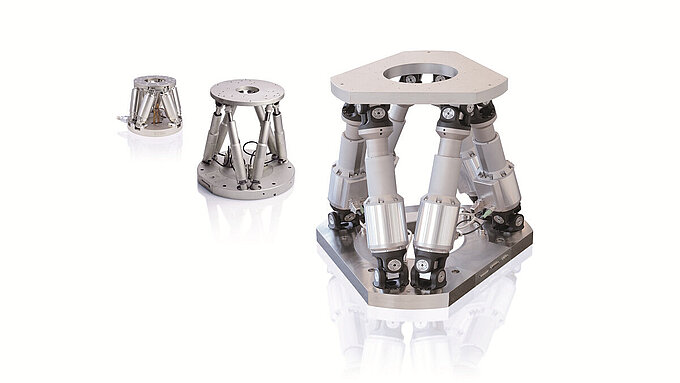
多轴定位器
六足位移台平台适用于在所有六个自由度(即三根线性轴和三根旋转轴)实现负载的准确定位和校准。
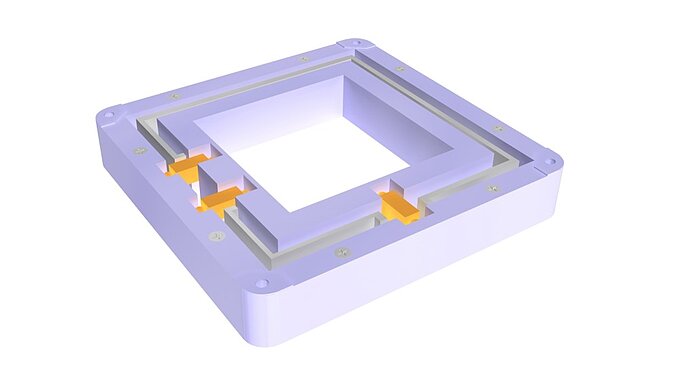
并联运动压电陶瓷定位系统
在多轴并联系统中,所有促动器直接作用于单一运动平台。
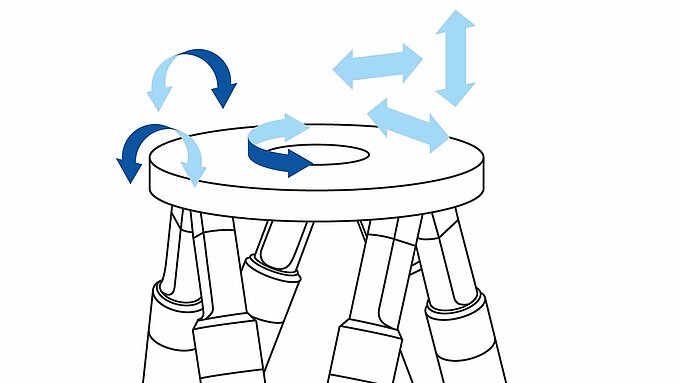
并联运动
在多轴并联系统中,所有促动器直接作用于单一运动平台。这意味着所有轴都被设计成具有相同的动态特性,从而显著减小移动质量。六轴用于在六个自由度上(即三条线性轴和三条旋转轴)实现负载的移动和精准定位、校准以及移置。